In the world of manufacturing, the choice of materials plays a key role in determining the efficiency and energy consumption of the production process. Among various materials, metals have long been a staple in metalworking and product manufacturing due to their unique properties, including strength, durability, and versatility. However, a pertinent question arises: Do metals make production more energy intensive? To answer this question, we must delve deeper into the properties of metals, the processes involved in metalworking, and the impact on the energy consumption of product manufacturing.
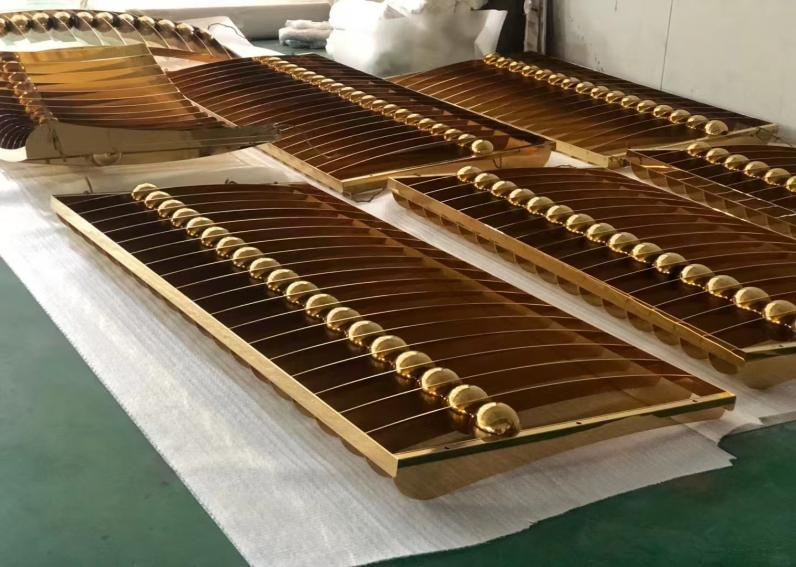
Properties of Metals
Metals have properties such as high thermal and electrical conductivity, ductility and tensile strength. These properties make them ideal for applications ranging from automotive parts to electronic devices. However, the energy required to extract, process and shape metals can be significant. The production of metals, especially through methods such as mining and smelting, is energy intensive. For example, it is well known that aluminum production consumes a lot of electricity, mainly because of the electrolysis process required to extract aluminum from aluminum ore.
Metal Processing Technology
Metalworking encompasses a variety of techniques used to work metal into desired shapes and forms. Common processes include casting, forging, welding, and machining. Each method has its own energy requirements. For example, forging involves heating the metal to high temperatures and then shaping it, which results in increased energy consumption. Conversely, processes such as machining can be more energy efficient, depending on the type of machinery used and the complexity of the product being manufactured.
The energy efficiency of metalworking processes can also be impacted by technological advances. Modern manufacturing techniques such as additive manufacturing (3D printing) and computer numerical control (CNC) machining can reduce energy consumption by optimizing material use and reducing waste. These innovations can lead to more sustainable methods of metalworking, ultimately impacting the overall energy footprint of product manufacturing.
Impact on production energy consumption
When considering whether metals make production more energy intensive, the entire life cycle of the product must be evaluated. While the initial stages of metal extraction and processing can require a lot of energy, the durability and longevity of metal products can offset these initial costs. Metal products generally have a longer lifespan than products made from other materials, which can reduce energy consumption over time due to less frequent replacement and repair.
Furthermore, the recyclability of metals plays a crucial role in energy efficiency. Recycling metals generally requires much less energy than producing new metals from raw materials. For example, recycling aluminum can save up to 95% of the energy required for primary production. This aspect highlights the importance of sustainable practices in metal processing and product manufacturing, as it can reduce overall energy consumption and reduce environmental impact.
In summary, while the initial energy requirements of metal mining and processing may be high, the overall impact of metals on production energy is multifaceted. The durability, longevity, and recyclability of metal products contribute to lifecycle energy efficiency. As technology continues to improve, the energy consumption associated with metalworking processes may decrease, making metals a more viable option for sustainable product manufacturing. Ultimately, whether metals improve production energy efficiency is not a simple question; it requires a comprehensive understanding of the entire manufacturing process and the benefits that metals can provide in the long term.
Post time: Dec-17-2024