Manufacturing metal products is a complex and delicate process, which starts from the extraction and smelting of raw materials, and then goes through several stages of processing, finally presenting itself as a variety of metal products commonly seen in our daily lives. Each stage contains unique technology and craftsmanship, embedding a combination of science and art.
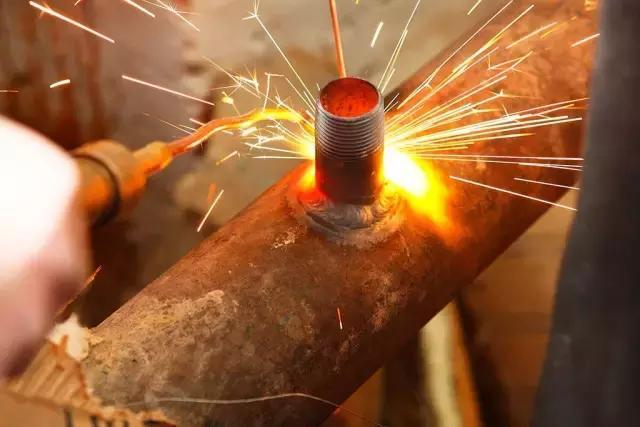
Smelting: the key to metal purification
The manufacture of metal products begins with the refining and smelting of the ore. After the ore has been mined, it must be smelted to remove impurities and extract the pure metal. The common smelting methods used in this process include blast furnace smelting and electrolysis. In the case of steel, for example, iron ore needs to be reacted with coke at high temperatures to produce pig iron, which is then further purified into steel. This stage focuses on temperature control and precise regulation of chemical reactions to ensure the purity and quality of the metal.
Casting and Forging: Initial Formation of Shapes
After smelting, the metal usually enters the casting or forging stage, where it is initially formed into its shape. Casting involves pouring molten metal into a mould of a specific shape to be cooled and formed, whereas forging changes the shape and structure of the metal by heating it and then hammering it. Both processes have their advantages, with casting being suitable for complex geometries and forging enhancing the toughness and strength of the metal.
Cold working: fine shaping and dimensional control
After casting or forging, the metal undergoes cold working processes, such as rolling, stretching and stamping, to achieve more precise dimensions and shapes. Rolling changes the thickness of the metal by repeatedly squeezing it, stretching is used to produce long, thin metal products, and stamping is often used to create complex sheet structures. These cold working processes require an extremely high degree of precision, and the accuracy of the machines and the skilfulness of the operating techniques have a direct impact on the quality of the final product.
Heat treatment: optimising metal properties
Heat treatment is an indispensable step in the process of optimising the physical properties of metals, such as hardness, toughness and wear resistance. Through heating and cooling operations such as quenching, tempering and annealing, the internal crystal structure of a metal can be adjusted to enhance its mechanical properties. The process goes beyond mere heating or cooling and involves precise control of time and temperature for optimum results.
Surface treatment: improving durability and aesthetics
After the basic processing of metal products is completed, surface treatment is required. This process includes electroplating, spraying, polishing, etc. The purpose is to enhance the corrosion resistance of the metal, improve aesthetics and service life. For example, stainless steel products are often polished to obtain a bright surface, or plated to increase corrosion resistance.
From smelting to finished products, the manufacture of metal products requires a series of complex and sophisticated process steps. Each step has its own unique technical requirements, and negligence in any detail can affect the quality of the finished product. Through these processes, metal is not just a cold material, but an indispensable part of our lives.
Post time: Oct-31-2024