As manufacturing continues to evolve, metal processes are moving towards greater precision and individualisation. In recent years, metal process innovation has become a hot topic in the industry, especially when it comes to customised solutions. Whether in the construction, automotive, aerospace, or consumer electronics sectors, more and more companies and individuals are demanding customised metal products, driving innovation and progress in metal process technology.
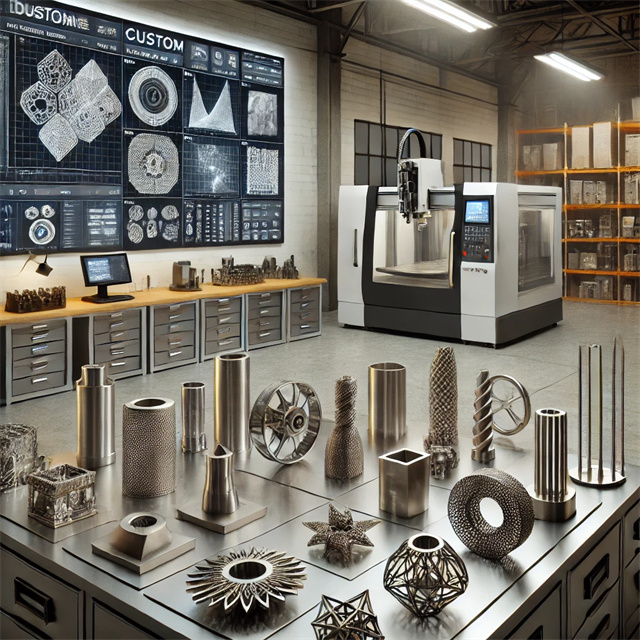
The traditional approach to metalworking tends to be standardised production, but today, consumers and businesses are demanding more and more uniqueness in product design, and personalisation is trending. This trend has prompted metalworking companies to continuously optimise their processes and achieve more flexible production capabilities through the introduction of advanced digital technologies, such as computer-aided design (CAD) and computer numerical control (CNC) systems.
3D printing technology is a big part of customised metal solutions. It allows for the rapid generation of complex metal parts, shortens production cycles, reduces costs, and allows for small-lot or even single-piece production. This technology not only improves productivity, but also increases material utilisation and reduces waste.
At the heart of metal process innovation lies a highly flexible and customised solution for the customer. Whether it is a unique shape, a complex structure or a combination of different materials, these customised requirements can be realised with modern metalworking technologies. Particularly in high-end manufacturing, the combination of individual requirements and high-precision machining technology allows for unprecedented flexibility and precision in metal products.
With the global focus on environmental protection, innovations in metal processes are also reflected in environmental protection and sustainability. Through innovative processes, companies are reducing waste, lowering energy consumption and making extensive use of renewable materials and recycled metal resources. This sustainable concept not only meets environmental requirements, but also earns companies wider market recognition.
In the future, metal process innovation will continue to drive the industry forward and provide better customised solutions for a wide range of industries. This not only enhances the added value of the products, but also brings a brand new experience to customers.
Personalised metal products: design and manufacture
As industrial technology advances and consumer demands become more and more individualised, personalised metalwork is making its mark in the world of design and manufacture. More than just standardised industrial materials, metal products can be uniquely tailored to the needs of different customers.
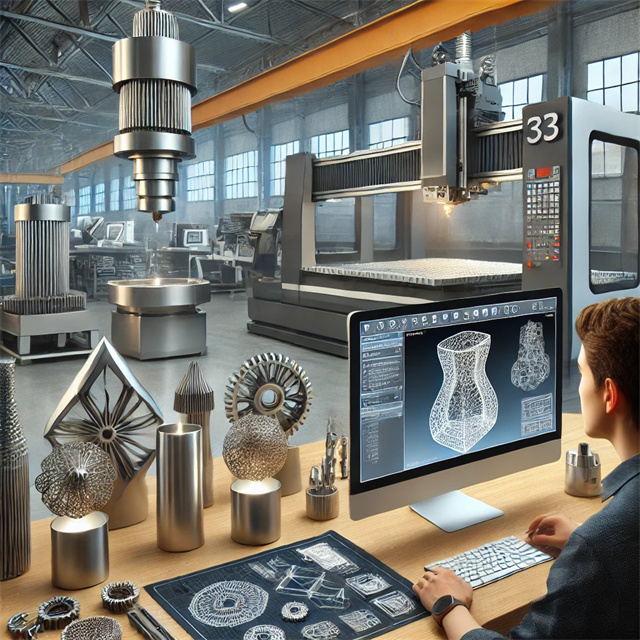
Nowadays, whether in the field of architecture, home decoration or industrial components, customers' design requirements for metal products are no longer limited to functionality, but focus more on the aesthetics and uniqueness of the design. With advanced CAD design software, companies can work closely with their customers to ensure that each metal product meets their unique needs and aesthetics.
Personalised design has a wide range of applications, covering everything from high-end home décor and artwork to machine parts and tools. Customers can choose from a range of personalised options in terms of material, shape, size and surface finish to suit their specific needs. This not only improves the functionality of the product but also enhances its visual appeal.
In order to manufacture personalised metal products, companies must rely on advanced metalworking technologies. Among these, numerically controlled machine tools (CNC) and laser cutting technology have become key tools. These technologies are capable of machining a wide range of metal materials, whether aluminium, stainless steel, or titanium alloys, with extreme precision and efficiency, achieving extremely high surface quality and detail.
With these technologies, the manufacturing process of personalised metal products has become much more flexible and the production cycle has been shortened considerably. Small-lot or even single-piece customisation models are better able to adapt to the rapid changes in the market and the diverse needs of customers.
With the continuous development of science and technology, the design and manufacture of personalised metal products will become more intelligent and diversified in the future. Artificial intelligence and big data analysis will provide designers with more creative sources to help them design personalised products that are more in line with market trends according to customers' needs and preferences.
The popularity of personalised metal products is not only a symbol of technological progress, but also reflects consumers' pursuit of uniqueness and beauty. As this trend continues to develop, the future of the metal product design and manufacturing field will undoubtedly be more brilliant.
Metal customisation specialists: a commitment to quality and service
In modern manufacturing, custom metalwork has become an integral part of many industries. Whether it's a complex mechanical component or a delicate building material, Custom Metal Specialists offers customers not only the product itself, but also a commitment to quality and service.
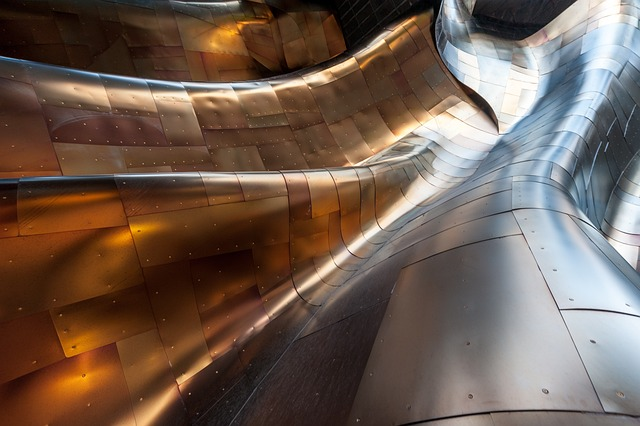
The essence of metal customisation is to provide tailor-made solutions based on the specific needs of the client. Each project is unique and the Bespoke Specialists work closely with clients to ensure that every detail meets their requirements. Whether it is the choice of material, the structural design, or the functionality of the product, it requires thorough communication and confirmation prior to production.
Quality control is crucial in the customisation process. From the selection of raw materials to every step of the production process, Custom Expertise strictly follows high standards to ensure that the final product meets or even exceeds customers' expectations.
Custom Metal Experts relies not only on advanced technological tools, but also on years of industry experience and expertise. With the aid of modern CNC equipment, craftsmanship still plays an important role in the manufacture of certain high-precision products. The combination of fine craftsmanship and modern technology enables the creation of highly artistic and functional metal products.
On top of this, many metal customisation companies have a comprehensive after-sales service system. Whether it is guidance on the use of the product after delivery, or subsequent maintenance and upgrades, customers are able to enjoy a full range of services. This commitment to service quality greatly enhances customer trust and satisfaction.
With the continuous development of metal craftsmanship, metal customisation specialists are not only satisfied with their current achievements, they are always committed to technological innovation and service upgrades. By continually introducing the latest production equipment, improving staff skills and keeping up with market demands, the bespoke metal industry is set to provide high-quality bespoke services to even more customers in the future.
With the global manufacturing industry moving towards efficiency, personalisation and sustainability, metal customisation specialists are creating more value for their customers with their expertise and commitment to service, as well as injecting new momentum into the industry's development.
Post time: Sep-19-2024