Metal products are widely used in construction, manufacturing, household and other fields, the quality requirements are particularly strict. To ensure the quality of metal products, enterprises must be strictly controlled from raw material procurement to the delivery of finished products in order to produce standard and durable products. Below is the whole process of quality assurance of metal products.
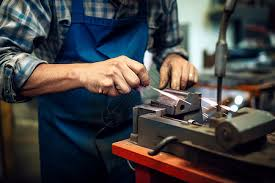
Selection and Inspection of Raw Materials
The quality of metal products depends on the quality of raw materials. Therefore, choosing good quality raw materials is the key to ensure the quality of finished products. When purchasing metal materials, enterprises need to ensure that they comply with relevant national or industry standards, such as the hardness, toughness, corrosion resistance and so on. At the same time, it is also necessary to strictly audit the qualifications of the supplier to ensure that the source of the purchased material is formal, quality assurance. After receiving the raw materials, it should also be stored before the inspection, to confirm its chemical composition, mechanical properties are up to standard.
Quality control of production process
In the production process, precision processing and strict quality control is the guarantee of the quality of metal products. In this link, the design and execution of production process is very important. Enterprises should adopt advanced equipment and technology to ensure that each process can meet the expected precision and quality requirements. During the production process, the inspection of key nodes should not be neglected, such as cutting, stamping, welding and other processes should be monitored in real time according to the regulations, so as to avoid substandard finished products due to process deviation. For complex products involving multiple processes, process optimisation and adjustment are also required to improve overall product quality.
Inspection and testing
After production, metal products need to go through a series of inspections and tests to ensure that their performance meets the standards. Common quality testing items include dimensional accuracy, surface finish, corrosion resistance, strength and so on. Enterprises should choose appropriate testing methods, such as non-destructive testing, tensile testing, impact testing, etc., according to the type of product to ensure the reliability and durability of the product in use. For certain high standard products, third-party testing and certification may also be required to further ensure product quality.
Packaging and transport
Metal products may also be damaged during transport and storage, so packaging is equally important. Suitable packaging can effectively prevent the product from being bumped, scratched and other damages during transport. According to the different shapes and specifications of the products, use appropriate protective measures, such as anti-rust oil, protective film, customised brackets, etc., to ensure that the products can reach the customers safely.
After-sales service and feedback
Quality assurance does not only stop at the production and delivery stage, after-sales service is also an important part. Enterprises should establish a perfect after-sales service system to deal with customer feedback in a timely manner and solve quality problems in the process of use. Through customer feedback, enterprises can also improve the production process in a timely manner, and continuously optimise product quality.
In short, from the selection of raw materials to the finished product inspection, packaging and after-sales service, the whole process of quality control of metal products is an important means for enterprises to enhance competitiveness and customer satisfaction.
Post time: Oct-24-2024